|
Author |
Message |
Aklogcabin
Member
|
# Posted: 5 Sep 2019 11:20
Reply
I consistently read posts concerning cabin foundations. For our cabin I stopped by a company that does power line installations. The gave me , free, some utility poles that they replaced. Cedar poles treated so they don’t rot. These will last a looooong time. And are easy to use. Mine go down 4’ then are about 3’ above grade. Leaving no hinge spot making things stronger. I was able to cut a shoulder into the top of the piling and bolt a 6â€x12†to them. A very strong connection. Used galvanized bolts. You are not building a home for full time dwelling. A complete concrete footing and cement or block walls is way overbuilding. And expensive. Much easier to pick up the phone and hire out but that ain’t cheap. I don’t have unlimited money to hire out work. And there is only one way to learn. Building a small structure like a cabin is great for learning basics. And I think most of us enjoy the experiences of learning new things that challenge us. Skids work great for smaller buildings like this. It would be easy to skirt your base to keep critters out. I also see where folks nailed or screwed 2 bys together. Much stronger and probably cheaper to find a local logger who has a sawmill and get whatever width or thickness beams you need. Best of luck have fun.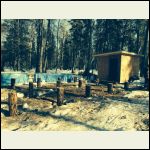 Cabin pilings
| 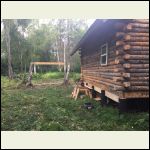 Pilings connected to beams
| 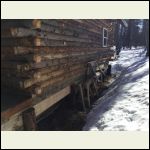 Cabin foundation
|  |
|
|
ICC
Member
|
# Posted: 5 Sep 2019 14:43
Reply
Quoting: Aklogcabin I also see where folks nailed or screwed 2 bys together. Much stronger and probably cheaper to find a local logger who has a sawmill and get whatever width or thickness beams you need.
Actually, when comparing the same species, the same grade and the same total actual thickness of materials, the built-up beam provides greater strength. Repetitive members used to support a load gain a 15% factor in the calculations. Repetitive members include the 2x material sandwiched to make a built-up beam, as well as the floor joists (3 or more), used to make a floor.
A triple 2x6 beam (actual thickness 4-1/2" will NOT be as strong as a 6x6 as the 6x6 will be thicker. But the difference in those examples is not very great, only about 6% greater strength. FYI the span tables for rafters and joists take the repetitive member factor into account.
Also, knots in a built-up beam only pass through one layer whereas a knot in solid timber can pass through the entire timber.
I won't get into the "it's only a cabin" argument that seems to be prevalent. I know of a couple of structures that began life as a part time use cabin and later became full-time residences. That is one reason a few (very few, it seems) locations have a special set of rules for a limited use recreation cabin and forbid conversion to full time, (PA for example).
|
|
Brettny
Member
|
# Posted: 6 Sep 2019 08:36
Reply
My house was once a summer house or a small small farm house. Theres also a cottage on the property thst was once a barn or garage both from 1932. After renovating both i refuse to make anything but plumb level and true with quality materials. Dont buy into the "its only a cabin", somt day tou may want to sell that cabin and something slapped together with junk isnt going to be appealing to a buyer.
I have a sawmill and will not me useing a single piece of wood for beams. They will be cut and built for one simple fact. A crack from drying or any other factor on a single piece beam will most likely be structural. A multi piece beam it wont be an issue. Milti piece beams also dont have all the same grain.
|
|
Aklogcabin
Member
|
# Posted: 6 Sep 2019 11:32 - Edited by: Aklogcabin
Reply
Holly cow. Try to suggest something and some want just challenge. Yes I agree that a built up beam done under factory controlled environment could provide up to 15%. I believe that in reality that the moisture content of the lumber is always an unknown on a construction site. Where exposure to rain n such. There are lumber mills here where the lumber is stored outside uncovered. Glue needs to be spread on the entire surface of the board and pressure applied so that the glue is forced into the grains of the wood. The pressure enhances the chemical bonding qualities of the glue. Most lumber I see , especially if it is over 12’ is pretty warped up. Could be soaking wet or dry or dirty. Especially if on a job site. Anyhow just my experience. Glued lots of lumber together and used beams I got from the local sawmill. The beam was way easier straighter. I feel that the natural forces that cause lumber to warp also cause them to work against each other . Yeppers just a cabin for me anyhow. As been stated weight is a big factor. Going to the cabin for weekend or full time dwelling. Don’t get me wrong. When I build our cabin I bought all new materials. And strived for the highest quality. Lots of folks shop for used or slightly damaged. But I suspect that most of us along the way have said its a cabin. I would love for this to be our full time home. Some , well me anyhow, folks can’t afford to hire out. Although I really enjoyed doing the work. But I had to learn most of the things I do cause I couldn’t afford to have someone else do it. I also enjoy it. And some folks need to build up as they can afford. Build or buy something that they can get into what they can afford and go from there. The largest complaint I read about is more government. Some folks that there is always a need for more laws because, oh my gosh , someone did something and it didn’t work out. Seems to me that hasn’t worked out so good to the point that the dream of buying a piece of land and building your dreams has been out priced by more government. Just my thoughts is all . By the way. Started out with a suggestion of cabin pilings. Since it is remote and everything has to be freighted. What do you think about the cabin I built?
|
|
Brettny
Member
|
# Posted: 6 Sep 2019 14:30
Reply
The cabin looks great. Any interior pics? Did you mill the D shaped logs your self?
|
|
ICC
Member
|
# Posted: 6 Sep 2019 15:38
Reply
Cabin looks quite nice.
Quoting: Aklogcabin built up beam done under factory controlled environment
I never intended to start an argument. I saw a point being made about using solid sawn beams, and those being called better than 2x's. I knew it is not true so took the time to try and spread a little of what I have learned from Professional Engineers over the years.
NOT a factory built beam. Simply a beam built on site from the same grade 2xwhatever dimensional lumber used for floor joists. NO glue. All splice points must be supported by a pier or post. Nails are used to basically just hold the layers in place; they provide no additional strength. I'll repeat, NO glue of any kind. Maybe some plywood patches if needed to bring the width out to match conventional dimensional metal brackets and clips. But we hardly ever would laminate a strip of plywood inbetween 2x as it is not needed and is difficult to calculate any strength factor in. NO glue because in the field the 2x may not lay together tight because of slight cupping, etc. NO glue and you figure load strength and deflection just on the actual 2x material used.
Build them on site on top of the piers or posts. No need for a crane, just carry the lumber to the piers and start assembling.
Factory glue-laminated beams like glulams and LVL are a totally different thing. They are absolute marvels of engineering. Normally mosy DIY'ers don't use them as they may need the use of a crane. In the controlled environment of a glulam factory, they will likely use machine stress graded lumber and have the very best layers on the top and bottom layers as that is where most of the bending stress occurs.
We usually use #2, S-P-F or Doug Fir. Lengths up to 16 feet, kiln dried and here everybody stores under cover. Nothing gets wet in the yards, or at least maybe just a little wind blown rain. Most of it is straight enough when we get it.
That is not just me making this up. That is what the PE I have worked with for decades would do.
|
|
NorthRick
Member
|
# Posted: 6 Sep 2019 15:56
Reply
Quoting: ICC Factory glue-laminated beams like glulams and LVL are a totally different thing. They are absolute marvels of engineering. Normally mosy DIY'ers don't use them as they may need the use of a crane.
Ha! I have two of them that will become a ridge beam roughly 24' off the ground. Remote site, no crane. I've got some ideas in my head on how we are going to do this but haven't settled on one. Fortunately, I have friends who think stuff like this is fun and are eager to help get them in place.
|
|
ICC
Member
|
# Posted: 6 Sep 2019 17:56
Reply
A lot of friends helps. If you have solid walls up you may be able to lift one end, then the other, using a block and tackle, engine hoist or ratchet winch or something. Temporarily fasten a pole to the wall to give enough height for the apparatus. If you have a large pulley block you could hang that from the post or pole on the end wall a few feet above the ridge beam saddle and use a good ratchet winch secured to the deck below and off to the side a bit. You don't want anybody under it when lifting.
|
|
|