. 1 . 2 . >> |
Author |
Message |
Ditchmonkey
Member
|
# Posted: 11 May 2016 12:40pm
Reply
I'm inclined to use corrugated metal roof panels for my 8x12 cottage as they seem inexpensive, durable, easy to install, and I like the look. I'm in a rainy area and have some concerns about the performance of these panels in wet weather. Installation instructions I have seen show that the screws should be placed in the valleys, which concerns me during winter rains. I was planning on using OSB and felt under the panels for additional water protection and sound dampening. Any thoughts on this?
|
|
bldginsp
Member
|
# Posted: 11 May 2016 01:30pm - Edited by: bldginsp
Reply
There seems to be two strains of thought on whether to put screws in the valley or on top of the ribs, whatever type of screwed metal roofing you are using. On the ribs, you haven't cut holes in the valleys where the water is, so it's less likely to leak. But the screws are not as secure. In the valley the screws are tight to the deck below, but better chance of a leak.
One solution is to use the solid closure strips that are shaped to fit under the roofing and fill the gaps. With those you can screw on the rib and get a tight cinch on the screws, at least where the closure strips are. You should have the closure strips top and bottom anyway to keep out critters.
Be sure to use the correct overlap at the joints of the panels. With corrugated they are supposed to overlap 1-1/2 ribs- so you have two ribs covered at each lap. You could overlap more for extra protection, and you can apply sealant in the overlap to try to seal it up.
DEFINITELY use 30 lb felt under the roofing if on a plywood deck. It's your last waterproof layer. If the slope is 2/12 or less, double the felt.
Get the good roof screws with the rubber gaskets, whatever you do.
|
|
Smawgunner
Member
|
# Posted: 11 May 2016 01:31pm
Reply
I used the metal panels from Lowes and they worked out perfectly. They were a special order item and they will cut them to length for you. The nails have a rubber gasket on them and will not leak. Been on my cabin for over a year and far so good.
|
|
Ditchmonkey
Member
|
# Posted: 11 May 2016 01:57pm
Reply
Quoting: bldginsp If the slope is 2/12 or less
Is this 2 feet over 12 span? My plan was going to be 2 feet over 10 span.
|
|
DaveBell
Moderator
|
# Posted: 11 May 2016 02:58pm - Edited by: DaveBell
Reply
Placing the screws in the flat and they are subjected to more water. Place them on the rib and they may not get proper compression of the gasket due to void under the rib. This can also distort panels.
My Plan
OSB for sound abatement.
Felt with upper edge overlap sealed with Butyl rubber sealant and stapled well.
Since I will have 12" Soffit, Panels will be 2" over Soffit edge.
Bead of Butyl rubber sealant applied to panel ridge and valley overlap.
Panels installed 1 1/2 ribs (like blgdinsp mentioned).
Holes drilled in valley.
Butyl rubber sealant applied to holes.
Screws installed by hand.
Per the factory techs, do not crush the rubber on the screws beyond the edge of the screw cap. Avoids early failure and leaking. That means they have to be hand tightened.
Corrugated Ridge Cap installed with Butyl rubber sealant and screws.
You may not see this kind of detail with Barns.
|
|
bldginsp
Member
|
# Posted: 11 May 2016 03:12pm
Reply
2/12 pitch is 2" in 12"
|
|
NorthRick
Member
|
# Posted: 11 May 2016 03:22pm
Reply
I've done metal and polycarbonate roofs on a few structures. A couple of observations:
1) Metal is less of a problem than the plastic panels.
2) The metal panels from the big box store, installed per the manufacturers directions (rubber gasket screws in the valleys and no less the minimum roof pitch specified) have been problem free.
3) Take shortcuts or install them on a roof flatter than recommended and will get some leaks.
4) The solid closure strips that Bldinsp mentioned are not so solid. Plastic panels with the strips and screws into the high points has been the most problematic roof so far. We get snow which will slid, either very slowly or all at once, and that pulls on the screw heads. Screws solidly into good sheathing don't move, ones in those strips do. The strips tend to split and no longer hold the screws well.
|
|
MtnDon
Member
|
# Posted: 11 May 2016 05:36pm - Edited by: MtnDon
Reply
Just a FWIW, the local metal roofing supplier here now sells screws that have a neoprene backed washer that has a deeper cup to the washer. It is impossible to over tighten them. The neoprene washer is compressed against the metal roofing and the cup of the washer prevents over compression. Easy install with a clutch equipped power driver.
|
|
Steve_S
Member
|
# Posted: 11 May 2016 06:57pm
Reply
I have to chime in here as I went through the same shtick... Installation of the screws depends on the metal profile or rib design... The A-Typical 'Ameri-cana' profile is the most common as linked below usually, have the screws through the rib itself.
REF: Ameri-Cana panel data
There are different types of Foam Closures. - The venting foam which looks like a complex mesh, allows for air flow, no water ingress and no bugs moving through it. - The sealing foam is heavy / dense and seals the space between the tin and you strapping.
* Venting between tin & sheathing provides a thermal break reducing heat transfer from tin to roof & a way for condensation to exit as opposed to being stuck.
To stop thermal transfer completely, you would have to use the Cool Roof method with the Foil Faced ISO on top of the sheathing and under the battens & counter battens !! Look at the instructions on the above link for more info
NOTE more info on the Cool Roof design can be found here @ The Texas Smart Roof™: The Coolest Roof in Texas !! This applies world wide, not just Texas.. There are similar articles at Building Sciences & Green Building Advisor but the link provided is a nice comprehensive article & description.
Neoprene washered screws have replaced the old Lead Washer types which always leaked after a year or two. You CANNOT crush / compress the washer, just cinched in tight and if your going through the rib, over-tightening will collapse the rib and deform the sheet (creating opportunity for leaks).
Lessons Learned TIP: - Once you have your layup done (strapping layer) stack all your tin on a flat surface make sure your edges are all even. - Measure from your roof 'peak' to centre of your strapping making sure they are consistent (typically 16"oc) - Measure from the top of your tin to centre of your strapping lines and make a pencil mark on both side edges of the tin. - Use a punch and dint the tin in nice straight lines across... - Use a drill with a 1/8" HSS bit and pre-drill your screw holes.
Now you will have straight & consistent 'screw lines' and by predrilling, you won't deform the ribs by trying to drill through with the screws & it makes lining the sheets up SO much easier. (If your roof isn't square, this is when you'll start sounding like an angry Drunken Sailor on a Saturday Night)
BTW: If you use Batten & Counter Batten method, you can make minor corrections for square without having to furtle with your roof or chopping tin to compensate (which looks bad btw).
Regardless of roof design, make sure you have drip flashings all around and that they are sealed.
Final Note... Felt is 'okay' but it does have a few issues under tin, especially if the tin is against it (that will void tin warranties by most companies). You would be better off spending a few extras Pesos and get Tyvek Roof Wrap or Dupont Roof Liner which will allow the sheathing to breath while shedding water / moisture away.
|
|
Ontario lakeside
Member
|
# Posted: 11 May 2016 08:34pm
Reply
We did a metal roof, our local manufactures recommendation was screws on the ridges. We installed T&G OSB, tar paper and 1X3 strapping. Do yourself a favour and get a nematic sheet metal cutter!! We have a low pitch (12 degrees) and no leaks so far.
|
|
rockies
Member
|
# Posted: 11 May 2016 08:53pm
Reply
Since you are doing a very simple shed roof with a low slope and you are in a rainy area I would recommend using a metal standing seam roof. If you order the sheets for the width of the roof you will be able to run one sheet right across the entire roof. Hidden fasteners are available so that when the next panel is locked in place it cover up the fasteners. You won't have to drill hundreds of holes like you would for the corrugated metal panels and you could order all the edge flashing and insect stops from the same manufacturer.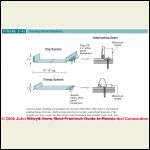 Sample Standing Seam Metal Roof
|  |  |  |
|
|
Littlecooner
Member
|
# Posted: 11 May 2016 10:02pm
Reply
Here is the 36 page guide for installation from the industry. Very informative reading.
http://www.homedepot.com/catalog/pdfImages/71/71b536d5-7179-4b4b-82e2-bd8e755c9e00.pd f
I am doing a very flat roof and an industrial supplier and installer recommended that I use the sealant tape on the overlap between each piece. This is a very small cost, as the tape is about $ 5 a roll in my part of the world. After using it, I feel very secure that my joints will not leak.
I hope this helps in your education of using metal roofing.
|
|
toyota_mdt_tech
Member
|
# Posted: 11 May 2016 10:59pm - Edited by: toyota_mdt_tech
Reply
I have a metal roof, it was installed professionally. I have the roof sheeting, and I laid on 15lb felt. Then left the rest to rhe roofer. I have a ridge cap vent. Its screwed into the valleys with large screws with heavy rubber washers. Never leaked, rock solid.
There is flashing over the facia at the rafter tails and the facia in the gable ends overlaps on top of the roofing keeping it water tight.
I cant hear any rain at all inside, not even during heavy downpour. I do have an attic and a insulated ceiling in my cabin.
|
|
AK Seabee
Member
|
# Posted: 12 May 2016 02:41am
Reply
stitch screws attach the sheets together on the rib with poly butyl tape on the joint strip. I place the structural screws directly adjacent to the rib, every rib, two feet on center for high wind areas. We go 4 feet on center for low wind areas.These are the recomendations of our local supplier.
A 2/12 pitch is pretty shallow for a metal roof. The square footage of your cabin roof is minimal. I would recomend using bituthane on the entire roof instead of just eaves and valleys. Then felt between the bituthane and tin. It will not leak. When the metal screws go through the bituthane they self seal.
I have used Sharkskin and Grace Ice and Water Shield. We have built quite a few roofs and not one has leaked.
|
|
Ditchmonkey
Member
|
# Posted: 12 May 2016 10:40am
Reply
Thanks AK Seabee, I like the sound of that technique. Since this is a shed-style roof, would you suggest some kind of flashing for the top. I'm not sure what kind of flashing is available for corrugated metal.
|
|
AK Seabee
Member
|
# Posted: 13 May 2016 12:24am
Reply
I buy my tin from "Magic Metals" here in Alaska. They bend it to the roof pitch and fascia (plumb cut or square cut). I am sure you can find a shop close by to bend your trim. The fascia trim and gable trim is common, if it were me I would have the peak trim bent to 12" down the slope and match the fascia trim. Look at usametaltrim.com for ideals
|
|
Littlecooner
Member
|
# Posted: 13 May 2016 08:24am
Reply
Ditchmonkey, please look at the link I posted for metal roofing. all this flashing options are shown on pages 9 and 10
|
|
AK Seabee
Member
|
# Posted: 14 May 2016 02:45am
Reply
I concur with LittleCooner, the link he provided is very informative.
|
|
Ditchmonkey
Member
|
# Posted: 14 May 2016 02:21pm
Reply
Any opinions on the delta rib pattern vs the wavy pattern?
|
|
MtnDon
Member
|
# Posted: 14 May 2016 02:57pm
Reply
They look different... 
|
|
Don_P
Member
|
# Posted: 14 May 2016 07:47pm - Edited by: Don_P
Reply
I think you'll find more trim options and all around support for the delta rib...but I'm installing 5v on a house now, so... they look different 
Our local metal shops can custom make just about any linear trim. There is a setup then footage charge so one stick hurts but it quickly becomes reasonable.
|
|
JDPugh
Member
|
# Posted: 19 May 2016 06:40pm
Reply
Something new to consider.....glue down metal roof panels. No screws at all: http://www.stealthbond.com/
|
|
Ditchmonkey
Member
|
# Posted: 20 May 2016 01:13pm
Reply
Quoting: JDPugh Something new to consider.....glue down metal roof panels.
Pretty sure I would glue myself to the roof with that stuff 
|
|
Ditchmonkey
Member
|
# Posted: 20 May 2016 02:43pm
Reply
Would you recommend that my 2x6 rafters be spaced at 16 inches, or will 24 inches be adequate? Half inch plywood or thicker?
|
|
NorthRick
Member
|
# Posted: 20 May 2016 02:47pm
Reply
24" OC, 7/16" plywood or OSB would be fine.
|
|
Don_P
Member
|
# Posted: 22 May 2016 07:21am
Reply
I prefer 5/8 for roof sheathing, gives the screws more to bite into.
I'm interested in manufacturer links that void warranty over felt and also instructions that show venting between metal and sheathing.
|
|
Steve_S
Member
|
# Posted: 22 May 2016 07:58am
Reply
My roofers wisely suggested 5/8's T&G OSB on my 2x8 rafters which are spaced @ 24oc. My cabin is 20x24 with a conventional gable roof, 24" overhang & cathedral ceiling inside. I used a Batten - Counter Batten design over the sheathing allowing for thermal separation & positive venting with a 2" airspace between sheathing & tin.
An observation noted: When the sun is heating up my Forest Green tin you can hear it expand (little pops) BUT I thought to test & see if airflow is actually working as intended... The vent slots (at the bottom) will pull a sheet of paper up and hold it, so it is sucking cooler air in and venting it at the top.
Whoever you get your tin from should be able to provide installation instructions for the particular product and the warranty info should outline what will negate the warranty.
As for the "I've always done it that way" commentary (opinions) take that advice with a bit of caution... 50% of those are correct & 50% are incorrect... you have to determine what is correct for you in your region/zone & for the particular product you are installing. And always follow what the manufacturer recommends as they know their product best and how it will perform under the various conditions.
|
|
Don_P
Member
|
# Posted: 22 May 2016 09:23am
Reply
That's what I'm hoping to see and learn from, what manufacturer source does that vented detail come from?
|
|
NorthRick
Member
|
# Posted: 22 May 2016 01:59pm - Edited by: NorthRick
Reply
From the Metal Sales instructions that Littlecooner posted a link to:
Metal Sales' panels are designed to be installed over open framing and/or directly over a wood substrate (minimum 5/8") with 30# felt moisture barrier (or an Ice and Water Shield when required by Local Building Codes).
So, according to them, felt is OK directly underneath the panels. They are also saying you need 5/8" roof sheathing, although I used 7/16" and the roof is holding up well.
|
|
KinAlberta
Member
|
# Posted: 22 May 2016 10:20pm - Edited by: KinAlberta
Reply
We have two old boathouses covered with standing seam metal, no strapping or sheathing at all underneath. Both buildings were built in the mid 1970s and have held up very well. This would not be suitable for a cabin due to the risk of noise.
Last year we had a garage and cabin 'professionally' done with regular metal roofing, screwed on the flat with neoprene washers and laid right over the old shingles. (I was very hesitant on this method until I read hundreds of posts by owners and installers saying that was quite ok and even in some suppliers' installation manuals.) That said, would a layer of roll roofing provide a good underlay to shed any water that gets last the screw holes.
|
|
. 1 . 2 . >> |