|
Author |
Message |
bobbotron
Member
|
# Posted: 30 Aug 2012 03:18pm
Reply
I enjoy doing wood working and metal working (with oxy acetylene welding). I can't do O/A in the city, as I'm pretty sure it'd void our house insurance and there's no smart place to put the torches.
I'd like to make a little workshop on my land in the country for this kind of stuff, the property starts at the top of a large hill, with a number of shelves down it, I thought the shop could be on one of the large shelves. I was wondering if any of you had suggestions for ways to build such a shop - I'm thinking long and somewhat narrow, with doors all along one side so it can be opened way up on nice days. Possibly tile for the floor for fire resistance, and metal siding. I realize it would probably be best to metal frame the shed, or make some walls out of concrete, but it would be quite challenging to get so much concrete down there! Another option could be cordwood or pole framing, (though with the latter I'm not so keen on having big PT posts in my workshop.) Building on less than even ground makes the foundation for heavier options more difficult, I think building it on piers would be easier, and invite less runnoff issues.
I will probably make a special external storage box for the O/A bottles/gear out of metal or concrete. I realize that O/A can be quite dangerous and take it seriously!
Anyway, I'm just dreaming at this point, was wondering if any of you have built a little welding shop in the woods and what it's like.
|
|
TomChum
Member
|
# Posted: 31 Aug 2012 07:02pm - Edited by: TomChum
Reply
Bobbo, You will be the only guy out there making special buildings for your O/A. Turn off the valves when you're not using the torch. A metal building, even with wood posts, is an OK place for OA setup. Be very careful with that torch outside when its dry out.
Tom
|
|
rayyy
Member
|
# Posted: 3 Sep 2012 04:16pm
Reply
I know you can never build big enough.I once had a nice 12x16 shed but soon out grew that.Built a 20x24 garage,still was crampt once all your equipment was in there.Years later I built a 30x36 barn mainly for parking the car and truck and tractor inside.I think now a 24x24 garage would be a decent size for your kind of hobby work.If you had to you could get one project car inside with ample working room around it.
|
|
bobbotron
Member
|
# Posted: 4 Sep 2012 09:24am
Reply
Hey guys,
Yeah, I'd definitely turn off the tanks when not in use, the right thing to do for so many reasons! 
I hear you about needing bigger and bigger shops, though I generally do small projects, brazing bicycles, artsy stuff. I have a 7x14 shed/shop at home that is at the "no more tools will fit" stage, but this is partially because it's also storing about 6 bikes...
Maybe I'll try to dream bigger for my next workshop. My new idea is to have a steel shed on the side of it for welding, and then a larger wood framed building beside it for non-fiery work.
|
|
TomChum
Member
|
# Posted: 4 Sep 2012 10:06am - Edited by: TomChum
Reply
Be careful building storage space for junk. Storing junk costs more than you think. Depending on what your projects are, you may need to have 'stuff' around. The good stuff enhances productivity, the bad stuff COSTS productivity. Usually your friends can see it but you can't.
There's junk and there's junque. May you be wise enough to know the difference. I see useful things, but I no longer "'see them' taking up space after they haven't made themselves useful for a couple years. The only way I can deal with it currently is to not have too much storage space. I'm working on it, but I'm in 'project mode' now, and all I see is new projects! Hard to assess junk sometimes.
Walls & doorways make for lost productivity. You're always wondering if that tool is in the other building. I wouldn't worry so much about 'wood framed' if most of what you see (from the welding area) is metal, drywall, or other non-combustible. You can cover wood with metal, easily. One good reason for having a welding room is to be able to exclude the flammable LIQUIDS from being stored there. No gas cans, gas powered machines, paint thinners, stacks of 2x4s.......
7X14 is too damn small. Don't go too big because you're currently cramped. Or design such that your space is expandable as needed.
|
|
exsailor
Member
|
# Posted: 4 Sep 2012 10:11am
Reply
My friend built a post and beam barn, basically by himself. He set the vertical posts and squared them. Next he run stringers to nail on green lumber locally cut. As the boards seasoned he went over and put batons over the cracks. It sealed up pretty nice and is one heck of an impressive structure. You could also nail tin over the stringers for walls but lumber would be cheaper. For what you want, lumber is probably the cheapest way to go. I would go for nothing smaller than 24x24 for a workshop. Good luck on your build and of course working with flammable gasses caution and safety are first.
|
|
bobbotron
Member
|
# Posted: 4 Sep 2012 04:20pm
Reply
Hey Tom. I hear you about storing junk, I try to be good about getting rid of stuff I don't need (I'm a cycling geek, the bikes aren't junk!) ;)
Currently there's a screen door in there that I think is borderline junk, definitely taking up a ton of floor real estate...
exclude the flammable LIQUIDS You mean I shouldn't bleed my O2 lines next to gas cans?! (Kidding, for the record I am extremely aware of safety/risk issues around oxygen!)
Here's something I made when I took a welding class two years ago. Great fun, once I get my O/A setup going I hope to make way more odd stuff like this. 
|
|
TomChum
Member
|
# Posted: 29 Oct 2012 04:05pm
Reply
Here ya go Bobbo, here's how they weld in the 3rd world. Some filipinos demonstrate a new welding invention they call a "pocket welder". You'll see why they call it a pocket welder during the video.
Skinny wires coming down from who-knows-where. Sometimes they have to put it in a bucket of water to cool it. They don't wear eye protection. Comments are interesting too, people making assertions based on their own opinions, that the filipinos specifically debunked in the video. It's entertaining viewing if you've ever stick-welded. Posted in 2007.
http://www.youtube.com/watch?v=KAplLEjTriE
|
|
bobbotron
Member
|
# Posted: 29 Oct 2012 04:09pm
Reply
Wacky! A+ for ingenuity. That's crazy, I wonder how safe it is?
That said:

|
|
MJW
Member
|
# Posted: 29 Oct 2012 04:25pm
Reply
How do they avoid getting welder's flash wearing no eye protection?
That is some painful stuff.
Crazy...
|
|
bobbotron
Member
|
# Posted: 30 Oct 2012 09:30am
Reply
For my building, I've discovered the awesomeness that is durock, micor, cheap tile and roxul insulation. I think I'm going to use some combination of this to create a spark resistant floor when I finally get around to this. I know it wont be perfect, but should be pretty good if I can't get a slab poured.
|
|
TomChum
Member
|
# Posted: 30 Oct 2012 07:40pm - Edited by: TomChum
Reply
FYI: Here's a pic of the floor of my shop. I weld all the time over it, the sparks dropping to this wood floor and rolling all around. It's Fir, with Varathane, and doesn't appear to be bothered by sparks. It has that old patina, but looks cool (I think).
Sometimes if it's going to be a longer job, I lay down a couple 1/2" cementboard sheets. The heat in any one spot is only for a few minutes, it's not like protecting a wall from an overheated woodstove for 4 hours. If I have to do anything where there's some real HEAT, I go do it on a concrete slab. Or if I have a longer job, where I will be welding a lot close to the floor, I go to the slab. I also have a fiberglas welding blanket (from Harbor freight) that I drape to block sparks.
I've had this shop for 6 years now. I don't worry about it much. The building was an ornamental iron works, that's where all the original scars on the floor are from, it looked like that when I got it.
It's 3/4" T&G fir ontop of "2x4s on end", so the floor is 4 1/4 inches thick, SOLID WOOD. In the old days that's all they had for fire protection, wood so thick that "burn-thru time" was a long time. My walls are concrete, and some interior are 2x4s with 5/8" drywall. The floor is original, probably about 70+ years old now, has had plenty of time to contribute to someone's Darwin Award.
My point is, don't worry so much about gathering all the right materials. It's not a big deal to protect a floor for occasional welding. Concrete floor is great, and almost any other floor, even plywood can be easily dealt with. Don't worry about your posts. Or just wrap them with sheetmetal or even drywall. Drywall is not fireproof, but it withstands fire for awhile, and thicker drywall has longer resistance. Drywall is the most significant fire protection since neighborhood fire departments. Drywall is not ignited by sparks, or a flailing torch. Worry more about flammable liquids, cardboard boxes, paper, rags, tarps etc.
Whenever you start to worry too much look at my floor pic and think; "hey this was used commercially for ornamental iron manufacturing, for 30+ years". It is obviously the WRONG kind of floor for commercial steel fab but it's stood the test of time. Either it's tougher than stupid, or stupid didn't work there but I bet it had all kinds of workers since the '30s when it was built.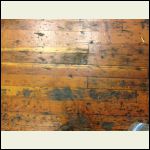 Wood floor of a welding shop
|  |  |  |
|
|
|