|
Author |
Message |
DaveBell
Moderator
|
# Posted: 11 Oct 2016 11:49am - Edited by: DaveBell
Reply
I'm thinking about making my own ridge beam onsite for a 20x32 cabin out of 2x8x10's and 2x8x12's using construction adhesive and bolts. Rafters would be 2x6x12's 16 inch on center. Looking for opinions.
EDIT: Thanks Don. I forgot to describe the support wall shown at 18 ft. How about Gorilla (expansion/hydraulic) glue?
|
|
MtnDon
Member
|
# Posted: 11 Oct 2016 02:30pm - Edited by: MtnDon
Reply
If you had supports columns centered under the splices it would work (everything sized properly of course). Construction adhesive has some creep when the glued together parts have shear forces involved. The typical construction adhesive also slowly degrades over time, although that may be measured in decades when everything is kept dry. Epoxy is too hard and does not adhere well enough to wood. Glues like Titebond also creep under load. Two part resorcinol glue might work but I don't know about how strong it is is the material does not fit tightly together. I don't know the gap filling properties, in other words.
The strength of through bolts is dependent upon the strength and integrity of the area above and below the bolt hole.
I don't believe there is a good method for making a DIY laminated beam for a clear span of 32 feet. Factory manufactured beams use special adhesives, heat and pressure.
|
|
MtnDon
Member
|
# Posted: 11 Oct 2016 05:24pm - Edited by: MtnDon
Reply
HOWEVER, with a column at the 18/14 foot point just size a nailed up lumber beam and see what sizes would be needed. Have a look at timbertoolbox. There is a beam calculator there. You might have toorder 18 or 20 foot 2x, but that can be done. maybe even get select structural grade. Also have the lumber dealer price out a laminated factory beam for a $ comparison.
|
|
DaveBell
Moderator
|
# Posted: 12 Oct 2016 05:59am
Reply
I haven't done the calculations yet but this was interesting.
https://www.youtube.com/watch?v=vG0wu1NV4QM
|
|
razmichael
Member
|
# Posted: 12 Oct 2016 02:33pm
Reply
As MtnDon suggested - make sure you also size and price out LVL beams. My beam is 24' (but supported at 16) and, although I do not remember the cost, it was much cheaper than I anticipated and delivered with a boom truck tight onto the supports. If I recall, I went with 3 LVLs each at 9.5". Could have used 2 but would have needed more depth thus taking away from headroom. With Sampson rafter hangers on the beam (and on the wall) and strapping across the top - it was quick to put up (although, as my design was a Gambrel roof - it took a lot more time to make the rafters).
|
|
bldginsp
Member
|
# Posted: 12 Oct 2016 03:03pm - Edited by: bldginsp
Reply
Does the mid support wall sit on a raised floor, if so, is there a pier under it? Roof load should always go directly to dirt.
Overlapping the 2xs only two feet is not enough, and I agree don't rely on glue. Construct or buy a 14 and an 18, land them both on a 4x4, put a concrete pier beneath the 4x4 if there is not one already. Or, put a beam beneath the 4x4 spanning between two piers. If it's on a slab you may need to cut a hole for a pier.
If there is no pier below the 4x4, and you don't want to put one in, you are effectively spanning the whole 32 feet anyway. You could manufacture a site-built truss for that, but you can't design it yourself. Might be worth having it engineered just because it would be easy to make on site and easy to transport the needed materials to the site, if that's an issue. A cooperative truss manufacturing company may be willing to design it for you cheaply with their software.
|
|
MtnDon
Member
|
# Posted: 12 Oct 2016 03:12pm - Edited by: MtnDon
Reply
I am not impressed. According to him it's a "pretty good strong beam". But there is no engineering to back it up and he admits it is not engineered. It appears he sized it to be approx the same size as a manufactured glulam that the glulam tables would carry the projected maximum load. . . that means nothing as a manufactured beam is more than just a stack of glued lumber. He states he uses #1 clear lumber... I see knots... clear has no knots, so it is hard to say what he used. As far as I am concerned it is just another "hillybilly" build, which is what he himself calls it in the video. DIY Youtube videos are a dime a dozen and that is about all many of them are worth, IMO.
|
|
bldginsp
Member
|
# Posted: 12 Oct 2016 10:44pm
Reply
That's quite a video. First he tells us that he is removing all the ceiling joists to make a vaulted ceiling, admits that this constitutes the removal of the basic structural elements supporting the roof, then proposes supporting the entire roof with an unengineered beam that looks good enough to him.
In the Middle Ages, stone masons built amazing cathedrals with little or no engineering calculation, they did it by eye and experience. Trouble is some of those beautiful cathedrals collapsed entirely in the first earthquake, sometimes killing most of the congregation. Trial and error isn't good enough when the safety of others is at stake, at least, not in my book.
|
|
MtnDon
Member
|
# Posted: 12 Oct 2016 11:18pm
Reply
Quoting: bldginsp Middle Ages, stone masons built amazing cathedrals with little or no engineering calculation
There was lots of trial and error. The wise masons learned and the buildings evolved and improved. That is how flying buttresses were developed.
|
|
DaveBell
Moderator
|
# Posted: 13 Oct 2016 08:33am
Reply
The walls will be on 4" slab w/ rebar. There will be rebar under the wall shown at the 18' mark. I found that the splices should be 4' so I changed that and increased the thickness to 10" on the drawing. It will be very difficult to get long materials, trucks, cranes, etc. to the property because it is so remote and the extremely mountainous roads. Hand building the ridge beam onsite is a solution, if the calculations support the approach. Just not sure yet. I wonder if it would be worthwhile to submit the idea to the local inspectors office to see what they say?
|
|
MtnDon
Member
|
# Posted: 13 Oct 2016 02:46pm
Reply
Quoting: DaveBell I wonder if it would be worthwhile to submit the idea to the local inspectors office to see what they say?
That raises the question of whether or not there will be inspections made, permits bought?
You should definitely ask before pursing the idea or building IF there will be permits/inspections. If you plan to build under the radar I believe you would be taking a mighty chance on something like this, if you are found out after the fact.
You haven't told us about what reg's you have to meet.
|
|
bldginsp
Member
|
# Posted: 13 Oct 2016 07:56pm
Reply
All the building department will tell you, at least, is to get the whole building engineered. At worst they'll bust you for construction without permits, if required in this situation (which is probable).
|
|
bldginsp
Member
|
# Posted: 13 Oct 2016 08:11pm
Reply
Quoting: MtnDon There was lots of trial and error. The wise masons learned and the buildings evolved and improved. That is how flying buttresses were developed. More to the point, timber framers have always worked off of trial and error and over the centuries came to know what would work and what not. But we don't have that pragmatic experience, or not to the extent they did, and they never used glued beams, but solid beams of lesser span.
DaveBell- your cabin is large enough that the structural support of it is a critical safety issue. If you have a significant snow load it's that much more important. Since transporting materials in is difficult, I'd say building your own beam or truss is the only choice unless you redesign the building to support it without large ceiling beams. I strongly suggest you get the engineering done somehow or other. You'll sleep better when it snows.
|
|
Steve_S
Member
|
# Posted: 14 Oct 2016 08:18am
Reply
As no one else asked, I will....
Why do you "need" a Ridge Beam ? Would a Ridge Board not do ? with Simpson Ties ? Even if doubled up with the joints staggered 4' - 6 ' ? 4x10 ? Is the roof design complex with many angles ?
I have laminated my own under the direction of Building Inspector for a previous reno... Used 3 - 2x10 and had 4' offsets to the joints, glued with PL Premium and spread over the wood with a fine flooring trowel and then nailed to schedule with 5, 3-1/2" spiral nails per side every 16". That went in to replace a support for the second floor on the old house (Balloon Frame - built in 1876)... While that was 26' in length it took 3 of us to heave it up and fit it into place and was a royal PITA (awkward spot and futzing required).
|
|
DaveBell
Moderator
|
# Posted: 14 Oct 2016 11:36am - Edited by: DaveBell
Reply
Quoting: Steve_S I have laminated my own under the direction of Building Inspector for a previous reno.
Steve, there wasn't a lot of support above for that approach. (FYI, nothing built yet, still designing)
I changed the footprint from 20x32 to 16x36. The beam had too many drawbacks. I am now calculating for a hybrid ridge board with roof 11/12 pitch, with rafter collar ties. The hybrid part will be laminating two ridge boards together to reach 36'. I won't need to meet "beam" support requirements due to the rafter collar ties, even though the ridge board will still be supported at either end. The increased pitch will allow 12' long rafter collar ties 1/3 the way up which will create a cathedral ceiling.
Someone may recommend something different for connecting the ridge boards (3 ea. 2x10x12's) else I'll just double them up with 4' overlap splices which sounds like your solution on the reno.
I'm working on the specs for the rafters.
Thanks Steve and everyone for the feedback. Let me know what you think of my new approach.
|
|
MtnDon
Member
|
# Posted: 14 Oct 2016 02:33pm - Edited by: MtnDon
Reply
A couple things.... First, the drawing is mislabeled. The component the drawing labels as a collar tie is actually a rafter tie. That drawing has no collar ties shown and they are required by code. An alternative though, is to use metal straps nailed over the peak, on the same rafter pair collars would be used. nail them on over the sheathing is fine.
The drawing I have posted is more correct as to how to determine thee 1/3 distance. That drawing also indicates the correct, allowable placement for the collar ties. Many folks confuse rafter ties and collar ties. The original posted drawing is not the first incorrect one I have seen on the infallible internet.
A collar tie is placed near the top of the rafter triangle to help keep the peak together under high wind conditions. The lower rafter tie is there to prevent wall spread.
One more thing... if the rafters are raised from the lowest, ceiling joist position a correction factor may have to be applied to the rafter size selected. As the rafter tie is elevated new and unplanned for forces are applied to the rafter. This will mean that much of an lift will require a larger section rafter. See the IRC here... The details are in the footnotes.... READ THE FOOTNOTES when using IRC tables as they are there for good reasons. [scroll down to table R802.5.1(1)]
************
A ridge BOARD is nothing special. It is not structural. You could build a rafter roof without any board at all. It's main purpose is to make the roof easier to assemble. It holds the rafter peaks in the proper places, spaced correctly. So it could be several pieces.Splices don't have to be anything fancy. Positioning ridge board splice between rafters and scabbing with a piece of plywood on each side works and is simple to do. No fancy cuts required. Of course that is assuming the ridge board will be hidden from plain site, which is the usual way. The board should be as wide as the surface of the slant cut that makes the rafter point. It could be two boards one above the other. We want to be sure the entire slant cut at the peak is fully supported to help prevent loads from causes splits to form.
A ridge BEAM is a totally different item. It is structural and requires proper engineered design.
Rafter specs come from readily available tables in the building codes as well as other sources. There are online calculators that are simple enough to use. You need to know the species and grade of lumber to be used as well as the ground snow load for the project site.
The second image (one of Don_P's) illustrates a stacked ridge board to provide full cut face support. The ridge board could extend below the rafter edge . collar ties vs rafter ties
| 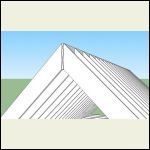 one of Don_P's images
|  |  |
|
|
bldginsp
Member
|
# Posted: 14 Oct 2016 04:23pm
Reply
The basic difference between a ridge board and ridge beam is that a board does not support the roof weight, so that must happen with rafter ties supporting the rafters as triangles. A ridge beam does support the roof weight. The weight of the rafters rests on the beam (or half of it, the rest on the walls) and the beam must be engineered for its span and calculated roof load (snow). Also, where the ridge beam is supported by posts the footings underneath the posts must be large enough to support the concentrated point load delivered by the beam. Ridge beams allow true vaulted ceilings but are more costly than a standard ridge board and rafter tie setup. A compromise is to vault the ceiling and leave the rafter ties exposed, place them on four foot centers. Or use steel rafter ties as in the photo here. The ridge "beam" in that photo does not function as a beam at all, it's really just a ridge board, it's just there for looks.
|
|
KinAlberta
Member
|
# Posted: 14 Oct 2016 09:49pm - Edited by: KinAlberta
Reply
I've come across a couple photos where three beams were used. A ridge beam plus parallel beams bisecting either side. Any thoughts on that?
Something like this but of sawn / dimensional lumber:
 http://www.explodedhome.com/wp-content/uploads/2014/09/Ridge-beam-in-Cabin-ceiling.jp g
Also, do renovators putting beams under an existing ridge board ever mix wood dimensions to maximize the depth given the rise on the rafter. Eg. 2x14 in the centre with 2x12s on either side (down slope).
Also I saw a photo on the Internet of an old European building where the bottom of the beam wasn't just three boards evenly laid side by side but offset slightly and the edges had a routered look (but it likely predated routers by a hundred years). Looked really good compared to the simple square/box look.
|
|
bldginsp
Member
|
# Posted: 15 Oct 2016 02:05pm - Edited by: bldginsp
Reply
The beams running mid-span to the rafters are called purlins. Note that the purlins in the photo have no support mid-span, so the engineering for such a roof needs to be carefully worked out beforehand.
Don't understand the second question.
Routers were originally hand tools used to put details on the edge of boards, then they made electric ones. The hand variety have been around for centuries if not millennia. It's just a scraper with a shaped knife.
|
|
KinAlberta
Member
|
# Posted: 17 Oct 2016 11:14am
Reply
Ok, I guess they were hand routered.
As for the laminating of a beam, all I was asking about was basically the use of different sized boards to build a beam.
|
|
bldginsp
Member
|
# Posted: 17 Oct 2016 08:13pm
Reply
I don't see why you could not use boards of differing widths in a laminated beam for aesthetic reasons. Complicates the glue up but not badly. It's all in the engineering- I imagine, but don't know, that the engineers would use only the largest single four-sided rectangular section that could be taken from the beam, regardless of how the offsets occurred. This is because beam strength is less about square area than it is about the ratio of width to height. But that doesn't really matter to you, I'm sure you are willing to use extra lumber for the desired profile
|
|
DaveBell
Moderator
|
# Posted: 17 Oct 2016 09:53pm - Edited by: DaveBell
Reply
Rafter Tie Length Calculations at Max Rafter Tie Height
|
|
DaveBell
Moderator
|
# Posted: 17 Oct 2016 10:08pm
Reply
What I found about Collar Ties.
Collar tie or "collar beam" is not generally required by code. They may or may not be required, depending on jurisdiction. (Not required by IRC but may be required locally) Collar ties are probably not needed if metal connectors were used to fasten the rafters to the ridge. (toe-nailed rafters need collar ties, else metal hangers on rafters) It is specified by engineering to assist with maintaining the rafters to the ridge board connection in high wind or imbalanced snow load areas. They do not help with wall spread.
|
|
DaveBell
Moderator
|
# Posted: 17 Oct 2016 10:18pm - Edited by: DaveBell
Reply
Rafters, using IRC R802.5.1(1) and the Rafter Span Adjustment Factor table in the footnote.
The footnote is required to calculate the rafter choice when a ceiling joist will not be used, such as when a rafter tie is desired to create a vaulted ceiling with a ridge board.
Another choice is a cathedral ceiling by using a ridge beam. Rafter ties could be added at any height since they are just for aesthetics as-is or used to create a vaulted ceiling.
Given a cabin size of 16 x 36, a 16’ Roof Span and 6/12 Pitch, the Rise is approx. 4’.
EDIT: I mixed my explanation work without using my choice for the cabin. All below has been changed to match my choices from the spreadsheet.
The 10’ rafter with 1’ overhang = 9’ Rafter Span.
Wanting to use a tie versus a ceiling joist, what grade and size lumber do I need per table R802.5.1(1) ?
The footnote Rafter Span Adjustment Factor (RSAF) HC/HR is read as 1 foot up/3 foot rise, 1 foot up/4 foot rise and so on to establish the factors.
The HC/HR of 1/3 = 33%, the maximum allowable height. The other HR/HC provided (1/4, 1/5, 1/6 represent lessor heights (25%, 20%, and 17%) respectively.
My height choice for rafter ties is the maximum, 16†in a 48†rise (16/48) which correlates to (HC/HR 1/3). (16/48 = 0.33, HC/HR of 1/3 = 0.33) HC/HR of 1/3 or 0.33 = RSAF of 0.67 from the table footnote.
You can already see that multiplying any rafter span on the table by the RSAF we found will reduce the span.
But you could also use the reciprocal to find the required span for a rafter tie.
(reciprocal of 0.67 is 0.33 or multiply the span by 1.33 to find the new total of the adjusted rafter tie span.
Rafter Span x reciprocal = Adjusted Rafter Span 9 x 1.33 = 11.97 ft
Converting decimal Adjusted Rafter Span to inches, 12 x 0.97 = 11.64 inches or 11’,11.64†12.0’ (rounding up)
So if I want to use a rafter tie 16†on a 4’ rise, I find items on the table equal to or greater than 12ft-0in.
If you look through the tables, you can find any 12’ or greater board 2x8, 2x10, 2x12, 16â€OC, 19.2†OC, 24†OC, etc.
I’m going to use the Table section 30psf Live Load and 10psf Dead Load, 16†O.C to find lumber greater than 12’.
2x6 Doug Fir #1 span is 12-9 2x6 Hem-Fir #1 span is 12-5 2x6 South Pine #2 span is 12-6 2x8 South Pine #3 span is 12-4
These are the closest choices that meet the specification while minimizing cost. There were also three suitable choices under the 24†O.C. section.
|
|
DaveBell
Moderator
|
# Posted: 18 Oct 2016 06:42am - Edited by: DaveBell
Reply
Choosing a 6/12 pitch for the 16x36 cabin..
The ridge board will be 2x8x12 Southern Pine #2.
The rafter will be 2x6x10 Southern Pine #2 which provides 9 ft span and 1 ft overhang, 16" O.C., attached with H1 or similar Simpson ties.
The rafter tie will be 2x6x12 Southern Pine #2, lag bolted to the rafter, installed at a height of 16".
|
|
MtnDon
Member
|
# Posted: 18 Oct 2016 10:35am - Edited by: MtnDon
Reply
You might want to rethink the use of lag bolts.
Nails are the code approved fastener; see table R802.5.1(9) for how many 16D common nails are required for pitch and snow load. Clinching a nail over increases it's strength rating by 25%. There is also an adjustment factor in the footnotes when the rafter tie is raised. Also note that most air nailers use the equivalent of box nails.You need more of them to do the job.
Connecting a rafter tie end to a rafter with multiple nails spreads the stress over a larger area. A lag bolt connection can fail quickly if a split occurs at the point of the single penetration.
Connection calculator is interesting. Check out the results when using a lag screw to connect a 1.5" thick rafter tie to a 1.5" thick rafter.
|
|
MtnDon
Member
|
# Posted: 18 Oct 2016 10:42am - Edited by: MtnDon
Reply
Bolts and nuts fare better. However when I compared 5 x 16D common nails, with SPF side and main members I get 600 lbs vs a 1/2 bolt with washers and nut providing 406 lbs. And that nail figure is with the nail ends protruding, NOT clinched over. The bolt connection is not as strong as the wood is the limiting factor.
Note: side member and main member can be initially confusing. An example may help. When nailing a sheet of OSB to a 2x joist, the OSB is the side member and the joist the main member. Or when nailing through a rafter tie into a rafter, the rafter tie is the side member and the rafter the main member.
|
|
bldginsp
Member
|
# Posted: 18 Oct 2016 02:02pm
Reply
I wonder how SDS screws would fare in the rafter/tie connection comparison. I've only seen them spec'd there a few times, but frequently on sole plate connections and ledgers. They seem to be very strong, but I've never seen a head to head comparison against 16Ds.
|
|
Steve_S
Member
|
# Posted: 18 Oct 2016 06:28pm
Reply
If you decide to use something like Simpson Strong Ties (I love Simpson products BTW - make life Sooo much easier) always use their screws / nails which are specific to the hardware. These are fully approved for use in my region and the connectors for Ridge Boards are the Cat's Meow..
This is what I am talking about here: https://embed.widencdn.net/img/ssttoolbox/gfhodsftyp/1200x630px/RR_layer.jpeg?quality =80&u=ydkg9w&crop=0
REF: https://www.strongtie.com/woodconnectors/category
On my build which the Building Inspector here thought I over built... but liked... I used that type of connector for the Ridge Board, on the Inside & Outside of my Gables I used the H1 Type of Connector. Served not only as a guide while installing the Ridge Board but also made a solid connection. My Ridge Board is 2x10. My Rafters (8/12 pitch) are 2x8 which I notched & blocked _AND_ used the H1 Ties as well on the outside off the wall...
H1 Tie: http://www.dhcsupplies.com/images/simpson/simpson_h1_sm.jpg
Because I blocked, notched & tied, that gave me an 8" "bay" for my rigid insulation above the top plate with my rigid boards snugged up tight. No Cold Spots ! I used the Simpson 1/4 Drive structural screws with my DeWalt driver (gotta be gentle on the trigger ! )
OF NOTE: Simpson makes a huge assortment of connectors & related hardware... As I used only SPF so I stuck with the conventional galvanised hardware.... They have an entire product family for PT Lumber and even a full suite for "Rough Cut", so a 2x bracket will be for 2" Exactly, not 1-1/2" for dressed lumber... ** Check with local building department before using Rough Cut - Too many do not allow it for their own idiotic reasons.... Some allow for Agricultural or Non-Habitable buildings. IF your in an area that permits Rough Cut from local mills, it may be worth considering BUT THERE ARE DRAWBACKS as you will have to trim pieces etc and that can be labour consuming if it varies a lot. It typically does up to 1/2" over nominal values... so a 2x6 could be 2-1/2 x 6-1/2 as opposed to dressed 1-1/2 x 5-1/2
BTW: Simpson has their info on a PDF and an Installer's Guide which outlines the various pieces and recommended screws, nails etc... Full List here - have a good peruse! https://www.strongtie.com/search?v=%3Aliterature-name-asc%3AliteratureCategory2%3ATec hnical+Bulletins&tab=literature
Nail Guns: I use a 34deg Stick Nailer (air) that handles up to 3-1/2" nails, love it, works a treat. I also occasionally a coil nailer BUT that can get pretty clumsy fast, especially in tight spots. Passloads are great if your way up and don't want lines around you (top of roof etc) BUT they are NOT cheap to feed fuel and charging extra batteries all the time is a royal PITA. Very expensive to buy as well. Best Bang for buck is my Stick Nailer... I didn't go nuts and buy a Bostitch unit either... Mega Pesos !
** Nail Gun Nails: Galvanised, Regular are no problem at all... Not outrageously expensive either. One supplier here also has nails with an adhesive coating that set's once the nail is in the wood... Those are a serious bugger to pull out ! With my Stick Nailer I just use boxes of Passload Compatible nails with the paper strip...
My Ridge Board: It is 28' long (2' hanging out of each gable with the fly rafters etc hanging off them) and I used 2, 14' boards and connected Clean-Straight @ centre (I do have a post that goes to ground under there) I made use of a pair of Simpson Connectors (one n ea side) for that as well which look similar to this below BUT made for the 9-1/2 board https://www.homehardware.ca/products/300/26493893.jpg
Building Inspector liked this as I also had additional metal work under it connecting to the beam running to ground level.
Just what I did and what I used and basically how I did it. Maybe it's a bit much or not enough, depends on who you ask and where they are building (Cali is nuts with all sorts of anti-quake requirements)... Maybe some or all could apply to your build, something to ponder upon.
Hope this helps... Steve
|
|
DaveBell
Moderator
|
# Posted: 18 Oct 2016 10:05pm - Edited by: DaveBell
Reply
The "Rafters, using IRC R802.5.1(1) and the Rafter Span Adjustment Factor" post above was done before I did the spreadsheet and included extra stuff as an explanation. What I failed to do was to use my choice (6/12 pitch, 9' rafter span) from the spreadsheet and run it through the calculations. So a bunch was changed and some extra info added.
I started with a 10' long rafter and will use a 10' rafter. The rafter span adjustment factor increases the 2x? dimension for applications not using a ceiling joist. MtnDon, Thanks for the input.
bldginsp, Thanks for the heads up on the SDS. I will check it out.
Steve_S, Much appreciated as always. I used H1 Simpson Strong Ties recently to build a rain shelter out in WV using 2x6 rafters on 2x8's. I'll post pics soon. I'll read your post again with coffee soon.
|
|
|