. 1 . 2 . >> |
Author |
Message |
optimistic
Member
|
# Posted: 7 Oct 2012 03:27pm
Reply
We drove for 3 and a half hours to see a huge fifth wheel but after seeing it, which was a great deal for price and size, we decided to forego the camper plan.
Instead, we have this idea - we have a friend that has a flatbed trailer (42ft) that was stripped from a camper (triple axle) and that we can have. We want to bring it to where we live in brooklyn, find a big warehouse that can house it close by (there are many abandoned ones around us with the whole outsourcing atrocity), and then build a cabin on it for the next few of months.
Pros - -it will be close to my house so I can go there whenever I have a few hours free - the warehouse will be heated, protected from the elements, and with electric power for my tools -I can bring help (my contractor and electrician) - buying materials will be easy and close - can build a cabin for the long haul instead of my plan on having a camper for a few years before a real build -no permit needed -customized everything so all the systems will be made for my plan of solar, water collection, and wood stove. -will be completely finish so I just need to plunk it there and I am done
Cons - - I need to find a warehouse that will let me do that for a reasonable price and that will be large enough to accommodate me - I will need to be very careful in the construction aspect to avoid a catastrophe on the road - I need to find someone that not only will be able to drive it up to my land (2.2 hours away) but that will also be crazy enough to pull it into my clearing which will be 1000ft in on a road without stone in winter.....
I am really excited about this idea because it will allow me to build faster and batter than I would have on site and this should be my cabin for good and not a part time solution (camper!)
I have a busy week but I hope to start looking for a warehouse next next week and see when I bring that trailer down. Then I will start to plan everything and begin the work....
A few "issues" that I will need to figure out -
-weight: I need to make sure I am not building it too heavy. I was thinking about doing the entire thing from steel studs, beside the rafters, but I need to look deeper into it - I want to keep the rain collection barrels (non-drinking) inside to avoid having them freeze on me but with my limited space they will have to be on top of the ceiling and two-three 55g drums filled with water weigh a lot...so no mistakes possible - probably my biggest design challenge: I really want to have a 3-4ft slide out across the living space which should be about 25 feet.
That is it for now. Update soon!
|
|
toyota_mdt_tech
Member
|
# Posted: 7 Oct 2012 04:10pm
Reply
I'd build an RV pad for the build. Make it bigger than your project. And make it to when you put in on the pad, you can block it up with cinder blocks (8 feet, some areas will be less) and then remove the axles, leave them under the rig in an area where its not in the way, same for the tongue and then build a retaining wall right off your concrete pad, build this up close to the end of the siding. Use some wide trim to close it off completely. Then you will have a nice dry crawlspace, no varmints will get in and under the flooring. The retaining and blocking can come in the spring. Just have a pad ready ahead of time. Nice and level. Grade it low enough to where finished unit, the siding is far enough above the soil. But a slope where it can be backed into the pad. Then shim and block.
A great way to find level is to use a water level. They take a large 5 gallon bucket, put a hose nipple on the bottom of it. Hook on a long piece of clear vinyl hose on it, will it with water and green food coloring. Set the bucket filled with green water on a shim where the water level at the top of the bucket is the desired height of the trailer frame. Now the long hose will have a column of water in it that will rise to the same spot. In other words, raise the end of the vinyl hose as you are under neath, the colored water column will be your level point. The end of the hose must be open to air, but a ball valve to close it so water doesnt escape. When you go to measure, raise it up, open the valve. Set your blocking up level this way, with large wedges just liek used in door shimming, except they are much larger and that goes on top of the cinder blocks below the frame.
I thought of doing almost the same thing. But you may consider just pulling the permit yourself, sub out the concrete, then have a framer give you a dried in shell. Then you just nibble on it as needed. But a permit means taxes, the trailer would be legal also but no taxes.
|
|
silverwaterlady
Member
|
# Posted: 7 Oct 2012 04:12pm - Edited by: silverwaterlady
Reply
First thing you need to do is to get the states towing laws from DOT. The height can't be more than 13'6' for bridges.Some of the bridges in your area are lower than that! You might need to get oversize permits(good luck on that) and go through weigh stations. if you are overweight on your axles you will have to pay a overweight fee that can run into the thosands.
|
|
toyota_mdt_tech
Member
|
# Posted: 7 Oct 2012 04:50pm
Reply
maybe even require a pilot car. 8'6" is usually the widest you can go before a special wide load permit is needed.
|
|
Anonymous
|
# Posted: 7 Oct 2012 05:57pm
Reply
STOP..........rethink.
|
|
Rob_O
|
# Posted: 7 Oct 2012 08:38pm
Reply
Quoting: Anonymous STOP..........rethink.
x2 on this, kill that idea before it grows and starts eating a hole in your wallet
|
|
Just
Member
|
# Posted: 7 Oct 2012 08:55pm
Reply
The up stairs water idea is not the way to go ...under ground tanks are much safer and a small pump will give you much better water pressure ..IMO
|
|
silverwaterlady
Member
|
# Posted: 7 Oct 2012 10:41pm
Reply
I agree with you Rob. Why not tent camp on your land(we did for 25 years) or buy a inexpensive trailer until you can afford to build a cabin.
|
|
TomChum
Member
|
# Posted: 8 Oct 2012 12:02am
Reply
Inexpensive trailer that takes no special effort to get it there. Re-sell when done.
|
|
optimistic
Member
|
# Posted: 8 Oct 2012 08:36am - Edited by: optimistic
Reply
I am not sure how much most of you spent on building your cabin but I believe that the cost of building the cabin on wheels will be 10-15k. Not to mention the fact that in my neck of the woods - permits are very expensive and debilitating. I rather not build a 144sqft cabin..
Can someone give a specific reason why I shouldn't do this?
I read: 1. "you need an over size permit to drive it...and a pilot car" - not true. As long as it is under 13'6" tall and 8'6" wide I do not need a permit. 2. "stop..rethink" 3. "hole in the wallet" - why? the only expenses I have that I would not have had if doing a real build are buying the trailer (I am getting it for pennies), rent a warehouse (three months will be $1500), and to rent someone to drive it which will be what - $700? But I save on building a foundation that for a comparable cabin would have been around $1700 (the smartest way for me is to get those steel posts installed because to dig and pour cement would save me about $500 but will cost me my health) and the permits.... Which are likely to be very very expensive - just stamped plans will run me a few thousands. Therefore, if anything, a cabin on wheels will be cheaper in the grand scheme of things.
A cabin on wheels can be made to look better than a cabin on the ground if you want to... look here for example.
https://picasaweb.google.com/104317431054100893074/8WideLoft
|
|
TheCabinCalls
Member
|
# Posted: 8 Oct 2012 09:33am
Reply
There is a lot of press about building small cabins on trailers. Do what you are comforable with...but as others are basically getting to here: DO YOUR HOMEWORK. Ask every question and plan wisely.
|
|
optimistic
Member
|
# Posted: 8 Oct 2012 10:07am
Reply
Thecabincalls - I agree with you 100%. As soon as I find a warehouse I will start in planning the build. The single biggest will be the slide out. Worst case, if it is really hard to achieve, I'll skip it and add an addition later on - on site.
|
|
optimistic
Member
|
# Posted: 8 Oct 2012 10:08am
Reply
Hhh.. Not sure where that smiley came from
|
|
wakeslayer
Member
|
# Posted: 8 Oct 2012 10:41am
Reply
The trailer you posted a link to is every bit of 12 feet tall if not more. It also weighs 13300lbs. Your base is 8 feet longer than that. You almost need to weigh every board and get your base weight figured out before you drive one screw into it. You need to make sure your frame will handle it, axles, tires... All that first. Building what you are talking about will be incredibly heavy. It was also designed with the original trailer in mind. Get an engineer buddy or someone else to go over this with you who can tell you if what you are doing is safe, if even possible. You could spend months and tons of money to find out you can barely tow it around the block, not to mention over 100 miles. Can it be turned around in your lot/driveway if you can get it there? That is a lot of weight to be offroading with.
i really think a cheap trailer to stay in while you build is a great idea. Take your time and do it right, whatever you do. Rome wasn't built in a day.
|
|
PA_Bound
Member
|
# Posted: 8 Oct 2012 10:58am
Reply
Just to echo everyone else... DO YOUR HOMEWORK, and get the right people to move it!
Here are a couple examples to consider. As you know, my cabin is a 14x40, amish built shed. It was built in a warehouse, and moved about 20 miles to my location. The width and height wasn't so much of a problem, but the length was.
1. Moving a cabin 40' long required a special trailer- to get it through the town where it was built and to turn it on some of the smaller, country roads (there is a reason why fire dept. ladder trucks require a tiller in the city). The open road in between was fine, but both ends were tricky. This trailer was special in that it had a second set of wheels, mounted at 90degrees to the standard road tires, that were electrically driven (see picture below). The driver could stop the rig, remotely lower these second wheels on the trailer, and move the trailer left-or-right without having to jockey the entire rig. I would never have gotten the cabin through some of the country roads without this feature.
2. Along the way we also nicked a bridge (thanks to a sharp turn in the road just passed the bridge), but fortunately the bridge was steel so it only just scratched the paint- paint that was even already scratched. The cabin did require some repair to about 3' of T111. We also required a telephone contractor for one turn to lift some telephone lines because when the trailer went around another tight turn, the back-end would have swung too far off the road and tore down some low telephone wires.
Moving a big cabin is not insurmountable, but get a few people to move it WHO KNOW WHAT THEY'RE DOING. This job is not for amateurs. The crew I hired mapped out and drove the route before hand, identified all the possible issues, and provided advise and services on how to overcome them. We even knew the bridge was going to be close, but there was no way around it and again knew any damage would be minimal.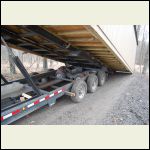 Transverse trailer wheels- a God-send for moving large items
|  |  |  |
|
|
groingo
Member
|
# Posted: 8 Oct 2012 10:59am - Edited by: groingo
Reply
I know exactly what you are going through, but in the end it is going to cost you waay more than you ever anticipated and will then take much longer as well. You have the bug to build something yourself to show yourself you can do it but if you actually sit down and make out the "LIST" showing both cost and benefits (Pros and Cons) of the trailer and the rolling cabin and why and (your answers must be completely honest, if not then you know it is the wrong decision), the results if the cons outweigh the positives or visa versa you will then have a solid direction. If you have any questions about the cabin on a trailer you need to speak to the expert, Jay at Tiny House.
|
|
TomChum
Member
|
# Posted: 8 Oct 2012 11:05am
Reply
Quoting: TomChum Inexpensive trailer that takes no special effort to get it there. Re-sell when done.
Optimistic, you need to settle down. You enjoy going through ideas more than the real thing. Get a low cost travel trailer, move out to your new land, start to enjoy it. Exercise will clear your mind. You will still have PLENTY of ideas, but they will be better ideas.
|
|
MtnDon
Member
|
# Posted: 8 Oct 2012 11:09am - Edited by: MtnDon
Reply
Do you have any idea of the GVW rating of that trailer frame and axle set?
The trailer was likely built in typical trailer fashion; lightweight materials, thin walls, thin paneling inside, aluminum sheet exterior and roof.
What materials do you envision for framing walls, roof? What exterior siding? Interior walls? Roof? It seems to me you could easily come up with more weight than the frame, axles and wheels/tires were originally designed to carry.
One thing that all the nice pictures on the internet do not convey, is how well the project turned out a few years down the road.
Just saying that this needs some serious feasibility study before renting space in a warehouse.
|
|
optimistic
Member
|
# Posted: 8 Oct 2012 11:36am
Reply
Hhh.. Not sure where that smiley came from
|
|
TheCabinCalls
Member
|
# Posted: 8 Oct 2012 11:51am - Edited by: TheCabinCalls
Reply
Just a thought to throw out there.
You could also use the warehouse to prefab the project so you have all the benefits of building close. But you could assemble the majority of it onsite...as to eliminate the cons that people are suggesting. The roof and other heavy elements can be added onsite. Even the truss work or anything that will affect height could be done there as well.
Most of the small cabins on trailers I have seen are not very large. However, I admire the optimism!
Thinking big picture here. One of the enjoyments of building a cabin is building it out on your land. You will miss this if 100% of your build is in a factory in Brooklyn. Just a thought
|
|
silverwaterlady
Member
|
# Posted: 8 Oct 2012 12:32pm
Reply
Don't forget about weight limits on bridges. If you go over the limit and get caught you will be spending tens of thosands of $ in fines!
|
|
silverwaterlady
Member
|
# Posted: 8 Oct 2012 12:44pm
Reply
Curious PA how much did it cost to move your shed 20 miles?
|
|
PA_Bound
Member
|
# Posted: 8 Oct 2012 02:58pm
Reply
I think all totaled it cost just shy of $1000. If I remember correctly, the standard delivery fee from the cabin builder was $300. Double that number again for the additional services to plan, coordinate and execute the difficult delivery. I was very happy to pay it however, as the delivery was pretty much turn-key with me doing almost nothing other than writing a check. The crew was from the local area, so they knew the cabins, local roads, alternative routes and other "gotchas" pretty well- even who to call about the telephone lines. I wasn't the first person they had done this for.
|
|
brokeneck
Member
|
# Posted: 8 Oct 2012 04:26pm
Reply
Optimistic -- Yes you are -- The trailer thing is way cool but has lots of possible catches -- weights - permits --access -- Why not use that sam wharehouse to build a prefab cabin -- done right ou could pre-wire and finish all the surface inside and out pullit apart and probably move it and have it reassembled in a weekend or two. Years ago my dad got a free 3 car garage -- he braced all the walls and pitched roof cut them into ections and had a friend move it to our house on a flatbed -- 2 weeks later the place was finished reroofed an painted --just a thought --
|
|
silverwaterlady
Member
|
# Posted: 8 Oct 2012 06:42pm
Reply
PA you did the right thing by hiring pros to move your shed. If they charge by the mile it was $50.00 per mile. How will you move your cabin on wheels Optimistic?
|
|
optimistic
Member
|
# Posted: 8 Oct 2012 08:36pm
Reply
Great input here!
Weight - that is a great point. a few things: I will try to get an estimate from an engineer but I already have a ball park because another company that sells houses on wheels - tumbleweedhouses.com - has one that is 8ft by 19ft so about half the size of what I will build and it weighs in at 5700lbs with wood frame. So mine should be about 12,000lbs... If I can do a steel frame I will cut a lot of the weight. But 12,000 lbs should not be an issue on bridges. As far as I can tell, in NY state, you can't have more than 22,400 pounds on one axle. I will have way less than that... Another thing - I will try to rent those portable scales to see how much it weighs before moving it anywhere.
Problem with a prefab cabin is permits, stamped plans, foundation, and so on. So in some areas it is easy to obtain but in upstate NY?? No way no how. That is why I won't do a prefab.
question - can I use regular metal studs (from HD for example) for the entire frame? Can it hold snow loads and so on?
Another crazy idea I had - b/c the cabin will be long and narrow I might have issues with having the heat from the wood stove reach the bedrooms on the opposite ends - the stove will be in the middle of the livings room. So I thought about just running PEX tubing under the two bedroom and bathroom. It will be a closed system with water that will come out of the wall next to the stove, connect to some copper hose, and rest on my wood burning stove which should heat the water that will then move throughout the system - heating the cabin. I will need to connect it to an expansion tank, pressure gauge, and temperature gauge, but it should be fairly easy. I can actually add some anti freeze to it to avoid emptying every time I leave there in winter. Also, if it gets too hot I will just move the copper hose from the stove... Thoughts?
|
|
optimistic
Member
|
# Posted: 8 Oct 2012 08:37pm
Reply
Silver - I will hire pros for sure. No way I am pulling this thing.
|
|
optimistic
Member
|
# Posted: 8 Oct 2012 08:52pm
Reply
I just realized that I missed some important posts -
Wakeslayer - I didn't see that it weighs 13300... wow. So mine should be a bit over that. this one is 39ft and mine is 42ft. So by simple calculation mine should way around 14,500lbs. I believe the triple axles of that trailer can carry 21,000lbs. The best will be if I can build from metal studs which will be much lighter but I will need to look into that. Ditto on the engineer. I will do that.
PAbound - 1. I agree. I will look into getting someone who has the right equipment. i won't spare cost here as this is a one shot deal and critical. Obviously I will insure it.
Groingo - Comparing camper to this is apples to oranges. This will be my cabin and not a temporary solution. A 35ft old camper will be at least 4k if I am lucky and will not be in good shape. I will then need to basically gut it (I won't stay in it like that), will build a roof over it, try to figure out the solar for it which won't be a walk in the park, and so on and so on with the end result -> temporary. I rather spend more now and have a finished product. I do appreciate all you guys thoughts though and I am grateful for your opinions.
Don- I agree. I already started a spreadsheet for costs. In terms of weight issues... I will try to find out GVW of the axles. Online most are 7k each but I will check further. I won't rent the warehouse before I have a plan and budget. From what I found so far - a warehouse should be around 600$ a month. But I might find a friend of a friend that could get me into one for free or for almost noting.
|
|
wakeslayer
Member
|
# Posted: 8 Oct 2012 09:26pm
Reply
I come up with right around 16000lbs GVW using your math. His rig is 34 feet not 39 feet.
|
|
optimistic
Member
|
# Posted: 8 Oct 2012 10:40pm
Reply
your right. my bad - it is 34. I am waiting to hear form him on the weight allowed on that trailer
|
|
. 1 . 2 . >> |