. 1 . 2 . >> |
Author |
Message |
fthurber
Member
|
# Posted: 3 Dec 2011 11:14am
Reply
I am seeing a lot of plywood & OSB used for walls and roofs and I am wondering why. Is it simply easier and faster to build that way? I am using 1X10's from the sawmill for my under-roof and walls (maybe ship-lap from the sawmill); it seems about the same price as the engineered wood and looks nice and does not off-gas formaldehyde.
|
|
neb
Member
|
# Posted: 3 Dec 2011 12:18pm
Reply
I would say that is just as good or better as a sheathing. In most cases people don't have the avalibility for such a product. There should be no differance and of course under lay is to make structure strong.
|
|
davestreck
Member
|
# Posted: 3 Dec 2011 04:51pm
Reply
We used 1x6 tongue and groove spruce from the local lumberyard. Plywood/OSB wasn't an option since all materials have to be carried in to the site by hand over some pretty rough country. Laid on at 45 degrees and nailed twice at every stud it provides just as much racking resistance as plywood, and was cheaper to boot. Plus, it looks so much better on the inside. More labor to install, but less waste and the scraps can be easily hatchet-split for kindling. Plus all cuts are easily made with a handsaw so the genny got used very little (mostly for just long rip cuts on the portable tablesaw)
All in all, I'd go with solid wood sheathing even if ply was an option.
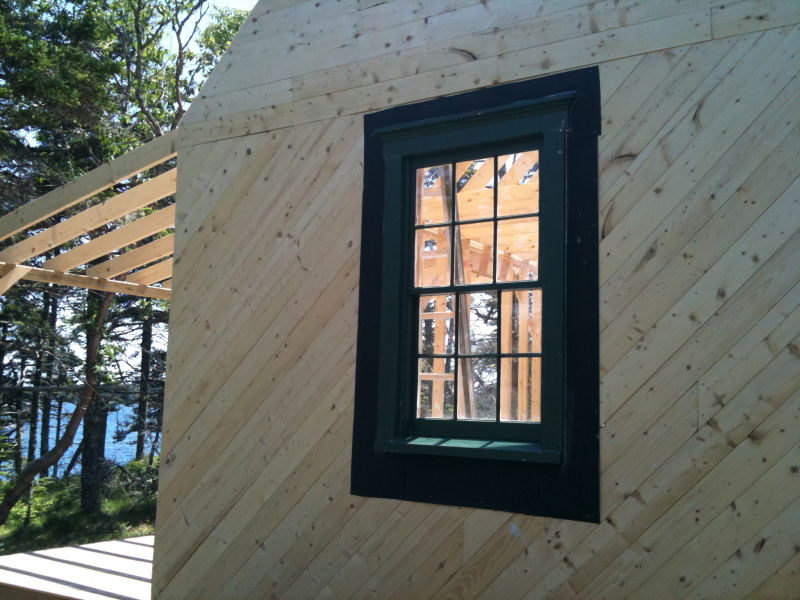
|
|
fthurber
Member
|
# Posted: 3 Dec 2011 04:52pm - Edited by: fthurber
Reply
Yes I could definitely see how plywood would stiffen a stick frame building but I try to do post & beam these days. I have done 3 cabin/sheds without any plywood or OSB but in my current project I had to use a bit of plywood for the subfloor so I would have a flat surface for some solid cherry flooring that a friend gave me...
|
|
Borrego
Member
|
# Posted: 3 Dec 2011 04:57pm
Reply
OSB: It took us about 20 years to get OSB right. The early stuff was unbelievably water sensitive. The edges swelled and the only thing you could do was to invest in a belt sander. Some of the cheap stuff today is still pretty bad. But if you shop well you can now get OSB with nail-holding characteristics as good as plywood's and OSB shear strength that just rocks (actually it doesn't rock... which is the point...). And it can rain on it and not swell. And we don't need big trees and it is much less expensive than plywood. Pretty awesome all things considered.
So what's the catch? There always is a catch. It does not breathe as well as plywood or redistribute water as well as plywood........
|
|
fthurber
Member
|
# Posted: 3 Dec 2011 08:47pm - Edited by: fthurber
Reply
OSB? Ick! Why bother when you can get real boards from the sawmill for about the same price or less. I don't want to spend time in a plastic cabin breathing OSB/plywood fumes when I can be breathing real pine scent. OSB look terrible also.
OSB seems like a way for giant corporations turn scrap wood and undersied trees into a product for mass-produced condos and such. Why use it in a prized cabin? Maybe for a outhouse...
Maybe I am just old fashioned and grouchy but you can have your manufactured woods...I'll stick to real wood.
|
|
MtnDon
Member
|
# Posted: 3 Dec 2011 09:19pm
Reply
There are two types of formaldehyde based resins and there are important differences in those resins and their use in wood panel products. The first important distinction is between urea-formaldehyde (UF) and phenol-formaldehyde (PF).
UF is more toxic and should be avoided at all costs in anything you put in your home.
PF is more water resistant and stable than UF, which means formaldehyde will offgas at lower levels and very slowly, but for a longer period of time. PF products are considered to be relatively hazard-free.
Most exterior plywoods and OSBs use PF. Unfortunately, many interior plywoods, MDFs (medium-density fiberboards), and particleboards contain urea-formaldehyde. So the exterior grades are probably fine to use, especially as in most intended uses the panels are on the outside and any possible gassing goes to the outside.
Newer OSB is a very good product. I have talked with engineers who now believe OSB is superior to plywood in many applications. OSB should not be exposed to the weather though. So for something like a roof overhang without soffit material, plywood should be used for the sheathing along the eve line.
I also know professional builders who have completely changed away from plywood as sub floor material and now use OSB exclusively. Their reason? With plywood and weather exposure before the building would get dried in there was the occassional need to replace a panel that got wet and delaminated. Using a quality OSB product has totally eliminated that problem.
More in the next posting.....
|
|
MtnDon
Member
|
# Posted: 3 Dec 2011 09:28pm - Edited by: MtnDon
Reply
This information is from the following website: http://mgacon0.tripod.com/plywood.htm It's a California construction firm website. There are popups, so be aware.
I'm reproducing the important data below. The absolute values given on that website have been "eyeballed" by a friend who is a licensed structural engineer and says they do look about right. This compares the traditional let in 1x4 wall bracing with plywood sheets.
The first image is the 1x4 let ins... Their calculations indicate it would take a force of 245 lbs applied laterally to the top plate to deform the wall. Let it be noted that the illustration has an inaccuracy. The 1x4 should also be let into the bottom and top plates for maximum strength from this method. There are also metal straps available for this, and Simpson has some T profile metal straps.
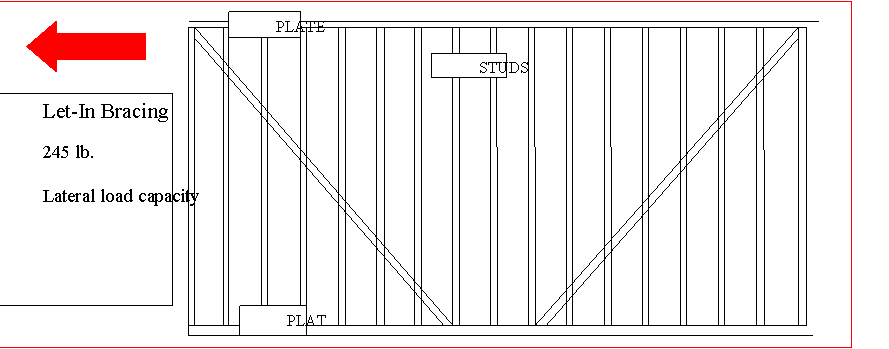
The next illustrated method is to use 1/2" plywood panels at just the corners. In between non structural insulating sheathing is used by some builders. The corner sheets are placed vertically and nailed according to code, 6" spacing on edges and 12" spacing in the panel field. This method is over 5X as strong as the 1x4 let in bracing.
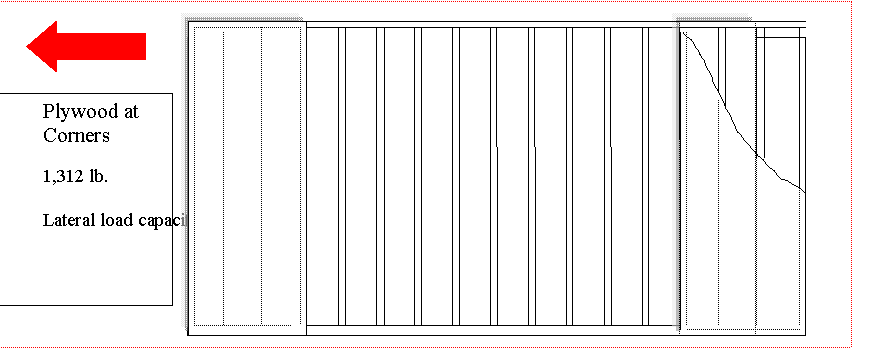
The third method illustrated is to use 7/16 or 1/2" 4x8 structural plywood or OSB sheets placed horizontally in an upper and a lower row. Again panels are nailed 6" on supported edges and 12" in the field. Note this example does not use any blocking at the horizontal seam between panels. A twenty foot long wall section like this will be 10X as strong as the wall with the 1x4 let ins, and almost double the strength of the wall with plywood panels at the corners only. Note that a problem with horizontal panels without blocking is that a force applied to the upper plate down the length of the wall can cause the upper panels to slide horizontally in relation to the lower panel.
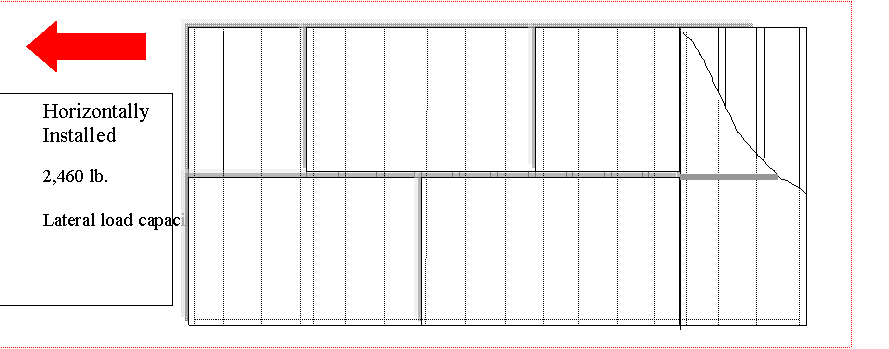
The fourth illustrated method is similar to number three; the plywood or OSB sheets are installed vertically. This permits all the panel edges to be nailed on 6" centers with 12" in the panel field. Because all the edges are nailed, this gains some strength. This wall construction calculates out to being more than 13X as strong as the 1x4 let ins.
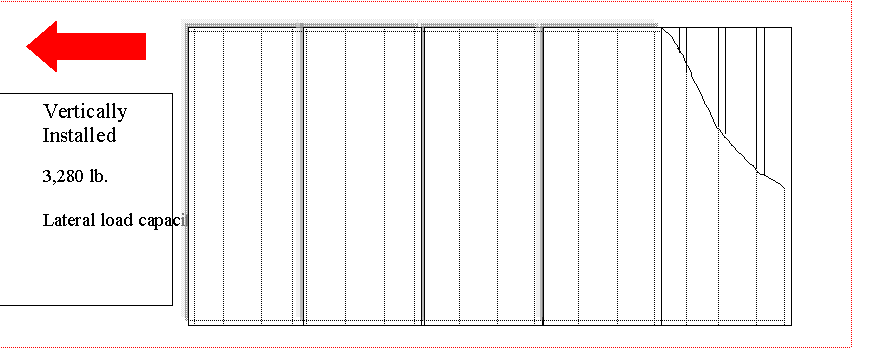
Note that if blocking is nailed in at the horizontal panel joint in illustration three, the horizontal panel placement will calculate out to be equal to the vertical panel placement.
So that's "Why all the OSB and plywood?"
The relative strengths would also apply to a roof structure; purlins compared to full sheathing. One difference is that roof sheathing is not blocked and that would reduce the strength gains of the panels as shown in the wall data. But it would still be miles ahead of a roof fitted with purlins and metal roofing.
As for roofing, one thing to keep in mind is that many metal panels roofing products are NOT rated as structural panels. That is they may buckle under sideways forces. Thus, many metal roofs with purlins instead of sheathing as not too strong when it comes to resisting strong winds.
|
|
Borrego
Member
|
# Posted: 3 Dec 2011 09:41pm
Reply
Quoting: SquidLips OSB? Ick! Why bother when you can get real boards from the sawmill for about the same price or less. I agree as an old fart myself. But the new OSB is soooo strong and as a builder we are actually forced to used OSB as it is called out by engineers nowadays due to it's strength. And it is waaay water resistant and vapor free today. I still think everything is overkilled in today's building world but it is what it is............
|
|
Borrego
Member
|
# Posted: 3 Dec 2011 09:42pm
Reply
And Mtn Don, you are da bomb. always got the facts!!!
|
|
MtnDon
Member
|
# Posted: 3 Dec 2011 09:50pm - Edited by: MtnDon
Reply
The reason 1x4's were chosen for the doagonal bracing is that is permitted under most building codes. California and WA state would generally be exceptions to that. The use of wider boards would provide more strength than the narrower boards. The use of more diagonal boards, as in a fully boarded wall, would also increase strength, but no wheres near the ability of a fully panel sheathed wall, floor or roof. The key to boards is to place them diagonally as illustrated in Davestrecks picture above. Also the use of T&G boards adds a measure of anti-racking strength as the T&G joints provide a considerable amount of friction which adds to the resistance.
|
|
Borrego
Member
|
# Posted: 3 Dec 2011 10:21pm
Reply
We have to nail off shear at 2" perimeter now, and get a special inspection from an independent inspector..... CA is going way overboard....
|
|
fthurber
Member
|
# Posted: 4 Dec 2011 07:06pm
Reply
I build the strength of my structures in the framing (post & beam) instead of in the siding. I am an old foggie and depending on OSB or plywood to hold your structure together just does not seem right. I guess I am just old-fashioned but structures built the old way with beams and planks held up just fine.
I guess the other problem is that OSB look horrible and seems unnatural.
|
|
fthurber
Member
|
# Posted: 4 Dec 2011 07:09pm
Reply
Another issue I have is that OSB and plywood is that it leaves you at the mercy of giant corporations. When I buy a plank at the sawmill I know what I am getting; it cannot be adulterated to enrich a corporate CEO. When I buy plywood or (heavens forbid) OSB I don't know what I am getting and have to trust the retailer. We got screwed on some "exterior" plywood that Lowe's sold us that warped during the first rainstorm but others have done well with their stuff so I don't know what to think.
It is hard to now what to think about OSB with the large range of quality it seems to have. OSB seems to be hated by many roofers because it does (or used to) not do well when wet. One roofer said this: "OSB Sucks !!! Period. only the cheap builders and the ignorannis will attempt to argue otherwise. " But other roofers on that forum said that OSB has improved: http://www.contractortalk.com/f15/plywood-vs-osb-18291/index3/
|
|
TomChum
Member
|
# Posted: 4 Dec 2011 08:08pm - Edited by: TomChum
Reply
OSB it makes efficient use of woodfibres of the entire log, it is a sensible use of resources. Dimensional lumber has much more waste per log. OSB actually makes good use of the waste of dimensional lumber. If OSB is not strong enough then you either have a "special" design you're trying to accomplish - OR - the design is "wrong" but its not OSB's fault. When the design is wrong I agree that OSB could "suck". Or in comparison to something cool like post&beam, it could suck, relatively. But its a good material to have available.
I used some OSB on my cabin, but covered it up completely. Leaving OSB visible is like "not using trim" - its functional but its not finished. I did leave OSB visible on the inside of my storage shed.
|
|
davestreck
Member
|
# Posted: 4 Dec 2011 08:33pm
Reply
This may be going off on a tangent (as well as being classic flame-bait), but I second Squid on the "local" aspect of real wood siding. Engineered woods have a lot going for them as far as maximum use of resources, shear strength, etc., but solid lumber is still a viable and (I believe) excellent choice. I think most people would be surprised at how "sustainable" most small "Mom-and-Pop" sawmills are. Here in the Northeast, we're talking about the use of -second and -third growth trees, and whatever part of the tree doesn't become a board gets used as mulch or animal bedding. Carbon-neutral, no chemicals involved, and all the money goes to local folks. That alone is a good argument for using post-and-beam construction with non-structural solid wood siding, at least for owner-built structures like barns and cabins.
That being said, conditions are different depending on where you live. New England is more forested now than it was 100 years ago (though not as much as it was 500 years ago), as a result of agriculture moving west and small farms reverting to woodland, so we're not talking about the wholesale clearcutting of virgin timber that happens elsewhere.
Your mileage may vary, but I live in an area where I can use cheap, local lumber with a clear conscience. My barn/workshop is made entirely of lumber that grew within 25 miles of my house. And at roughly $.50/BF beats Home Depot 2x4s and OSB hands down.
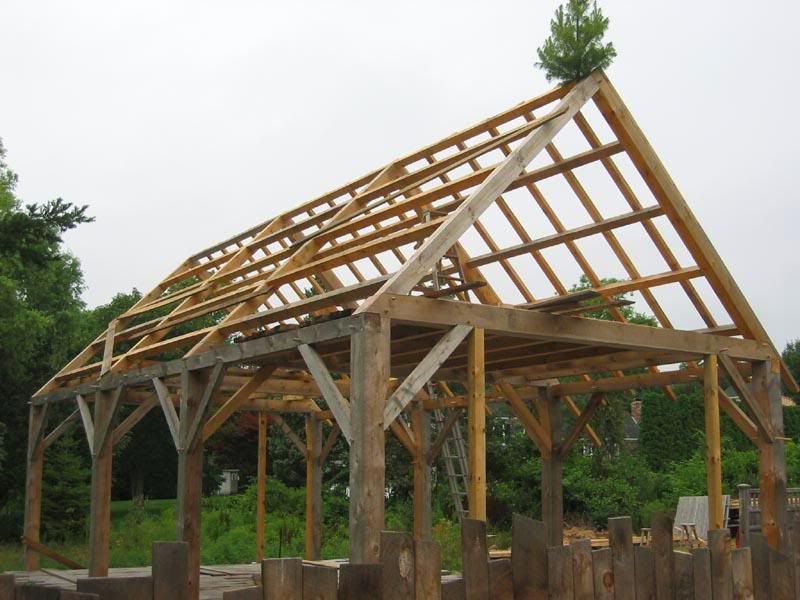
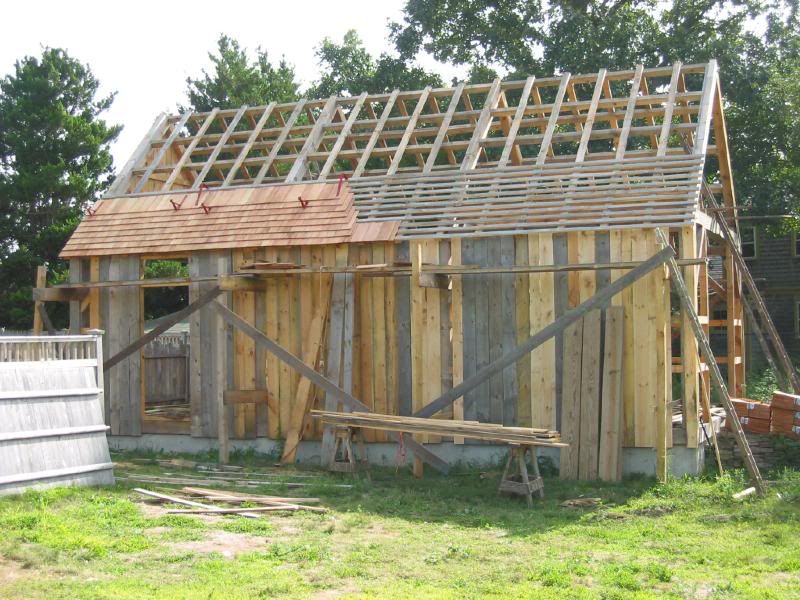
P.S. I hope no one takes offense at my opinions. I do believe that engineered lumber is an amazing technological achievement, and is superior to solid lumber in some ways and for some applications. I'm just thankful that real wood is still "good enough" to pass code when used properly. The day may come when it isn't.
|
|
fthurber
Member
|
# Posted: 4 Dec 2011 09:33pm - Edited by: fthurber
Reply
Wow; nice barn. Where did you get the plans? I need a barn really bad.
Anyway I second this opinion. Support your local sawmills instead of enriching the multi-nationals.
Here are some pix of my wife's studio. It was done with no engineered wood; all the wood was from the local mill. It was cheaper than the Big Box junk and the effect was much nicer.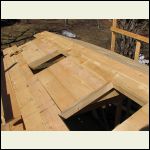 Roof being put up with 1x10 rough
| 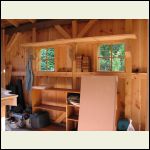 Interior
| 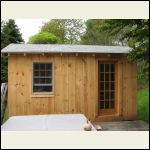 exterior
|  |
|
|
fthurber
Member
|
# Posted: 4 Dec 2011 10:04pm
Reply
I am not a total neo-luddite. I could see where plywood or even OSB would work very nicely for some spaces like a storage shed. I might use it for a boat shed or a firewood shed if I can find a reputable retailer.
It would also work for a living spaces if you paneled the inside with pine or some other wood so that the OSB was not exposed.
|
|
Martian
Member
|
# Posted: 5 Dec 2011 08:52am
Reply
Davestreck, are you aware there is a Red Cedar Shingle and Hand-split Shake Bureau? I wasn't until tasked with putting a new roof on a historic one-room schoolhouse 12 years back. The contract required following that set of standards. I really enjoyed the challenge of a cedar shingle roof; it was like putting together a jig-saw puzzle, without a picture, to meet all the requirements.
I like working with real wood, too. Mainly because it doesn't require handling heavy 4X8' sheets.
Tom
|
|
davestreck
Member
|
# Posted: 5 Dec 2011 12:29pm
Reply
Tom,
IIRC, the Cedar Shake and Shingle Bureau (or whatever they're called) specified overlapping courses of 30# felt paper between the skip-sheathing and the shingles. That seemed unnecessary (and possibly counter-productive) on an drafty, unheated barn, so I just laid the shingles right on the sheathing. Time will tell if I messed up, but its now ten years later and there's still not a single leak. Plus, I like seeing the underside of the shingles from inside, and I believe they get better ventilation that way too.
I doubt I'd do it that way on any insulated/residential building though.
|
|
Martian
Member
|
# Posted: 5 Dec 2011 01:37pm
Reply
Felt never goes directly under wood shingles; they need a breathing space.
What I did learn: put strips of cedar plank siding along the rake ends w/ the thick part out to kick the outboard edge of the roof up a little; three courses at drip edge w/the bottom two courses cut to length; nothing wider than 8" or narrower than 3"; no more than two nails per shingle; 1/4 to 3/8 spacing; and no three rain grooves aligned within 1 1/2" of each other.
Its quite a trick to put a good cedar roof on, but they will last 100 years if done right. Yours looks good and works; I wasn't being critical. I found it amusing how detailed they were.
Tom
|
|
AYP1909
Member
|
# Posted: 5 Dec 2011 03:34pm
Reply
I am going to second TomChum on this issue; OSB is a very efficient use of wood that would otherwise be wasted. In residential construction, it is very cost effective for the contractor to be able to lay and nail a numerous sheets in the time it would take to cut and nail individual pieces of shiplap.
|
|
Bridgeboy
|
# Posted: 5 Dec 2011 05:03pm
Reply
Hi SquidLips and others.
Beautiful studio building. I like post and beam construction where you can see the boards (sheathing) from the interior. What is the best was to insulate this type of building. Rigid insulation?
Thanks,
Bridgeboy
|
|
fthurber
Member
|
# Posted: 5 Dec 2011 06:45pm
Reply
Ah insulation. That is an unanswered question. Any suggestions? On my wife's studio we used two layers of boards with tar paper between. Not sure if this is working since the is floor drafty. Sort of doubt that it works.
I have not looked into rigid insulation yet.
|
|
MtnDon
Member
|
# Posted: 5 Dec 2011 07:00pm
Reply
Rigid sheet insulation is best used in sheets, over studs, not cut and inserted between studs. It's easier and more effective.
|
|
fthurber
Member
|
# Posted: 5 Dec 2011 08:25pm - Edited by: fthurber
Reply
Could I use sheet cork between two layers of wood? I know it is designed for floors but I wonder if I can use it on walls....weird idea but I am fairly unconventional...
|
|
MtnDon
Member
|
# Posted: 5 Dec 2011 08:48pm
Reply
Cork has an R value of about 3.1 per inch. I have no idea on how cost effective it would be compared to other materials. One inch of foam can range from about the same on up to an R-value of about 7 depending on type. Foil faced foam sheets provide an extra 2 or so IF the foil faces outward and there is an air space of about 3/4 to one inch between the foil and the exterior sheathing. That outer layer needs to be air sealed though.
|
|
fthurber
Member
|
# Posted: 6 Dec 2011 06:51pm
Reply
Maybe cork would breath better. My wife likes the idea of natural insulation but I wonder about rodents and bugs...
|
|
Martian
Member
|
# Posted: 7 Dec 2011 06:23am
Reply
Not according to the product details:
Contains No CFCs, VOCs, Penta-BDE's, Or Urea Formaldehyde
Tom
|
|
davestreck
Member
|
# Posted: 7 Dec 2011 05:03pm - Edited by: davestreck
Reply
Quoting: SquidLips Wow; nice barn. Where did you get the plans? I need a barn really bad.
I drew the plans myself, using a couple of books as references. The dimensions (18'x34') were determined by the maximum length beam the local mill could cut. Its an "English style" frame, as opposed to an American style, in that it has a continuous top-plate. Long walls were raised as complete bents and then the main beams were dropped on top, using a tying joint:
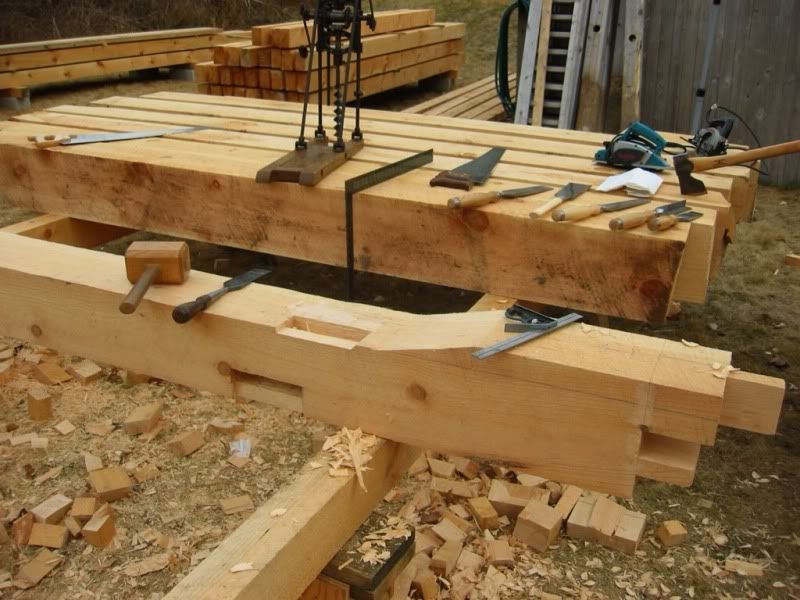
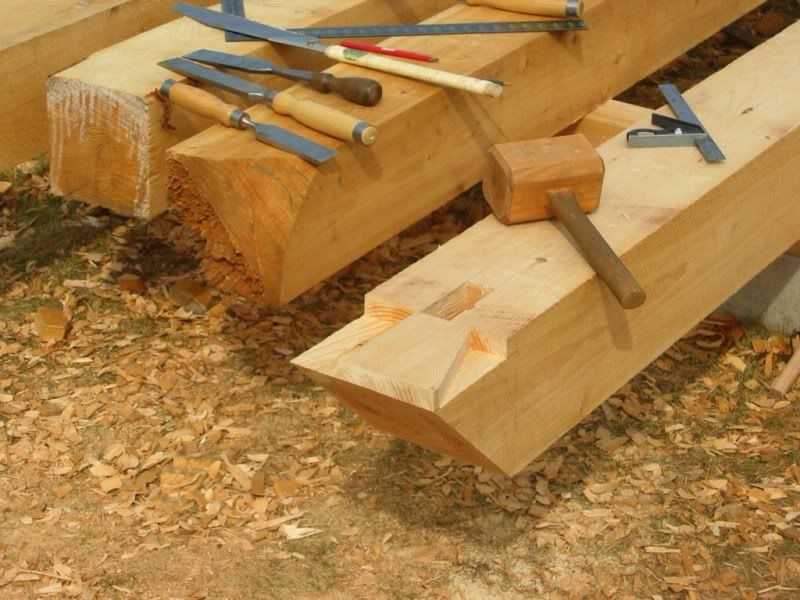
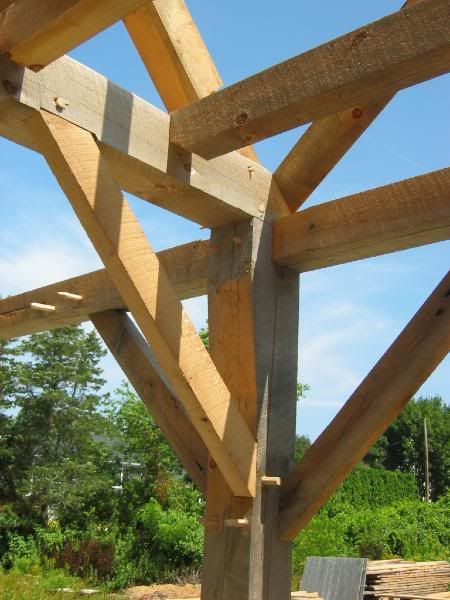
The frame is white pine with oak knee braces, and the pegs are handsplit black locust. Sheathing is roughsawn pine with cedar shingles.
|
|
. 1 . 2 . >> |